On 1 November 2019, the House of Commons' Business, Energy and Industrial Strategy Committee (BEIS Committee) published a further report on the safety of electrical goods in the UK (the "follow-up report"). This report follows an earlier report published in January 2018 which had highlighted key deficiencies in the product safety system in the UK, including the lack of a central product recall database and a national agency with independence and authority to deal with a major product safety challenge such as Whirlpool's tumble dryers.
We have summarised below the key points from the follow-up report and have identified a number of key practical takeaways to be aware of when dealing with a potential product safety issue.
Summary of the report
The report was highly critical of appliance manufacturer Whirlpool for failing to modify or replace faulty machines in good time, and of Whirlpool's attitude to product safety more generally. It also criticised the brand's use of non-disclosure agreements (NDA's) to silence consumers and focus on deflecting the concerns of customers and safety organisations.
The committee suggested Whirlpool crisis provided the Office for Product Safety and Standards (OPSS), set up in January 2018, with an opportunity to stamp its authority on product safety and address a major product safety issue. The BEIS Committee's report highlights a number of alleged failings on the part OPSS which, it says, call into question the OPSS' authority, independence and transparency:
- It did not question Whirlpool's over-optimistic estimates of the remaining unmodified machines and could not force Whirlpool to publish a full list of defective machines.
- Further criticism was made on the unconvincing report produced by the OPSS in which they reviewed the Whirlpool tumble dryers, the flawed conclusion that there was a low risk posed by the modified tumble dryers, and an incomplete risk assessment due to concerns over commercial confidentiality.
- More generally, the OPSS has not yet delivered a fully operational hub for consumers to register their electrical goods and access information on recalls, a comprehensive injury database or indelible marking for electrical goods.
- Finally, the report raised concerns over the inability of the OPSS to use civil sanctions for non-compliance with product safety standards and how it makes it a "toothless regulator".
As well as criticising Whirlpool and the OPSS, the BEIS Committee expressed concern that funding shortages for Local Trading Standards have not yet been addressed. Describing Local Trading Standards as “the eyes and ears” of the OPSS, the report notes that Local Trading Standards still struggle due to cuts in funding.
Practical takeaways
We have set out below the key practical points to take away from the report, when dealing with a product safety issue and assessing whether a recall is necessary:
- The report highlights the importance for product manufacturers of using the EU RAPEX methodology for making an objective safety risk assessment. It is clear from the report that it is the expectation of the UK regulator that this methodology is followed (although a number of methodologies are available). Details of this methodology can be found in the OPSS' Code of practice on consumer product safety related recalls and other corrective actions.
- The OPSS is likely to place greater scrutiny on the criteria for deciding what data to withhold because of commercial confidential concerns and what can be shared to improve product safety.
- It is important that product manufacturers are aware of what rights consumers have to request information from a manufacturer if a product malfunctions and how much information is shared with safety organisations, such as the Fire Service for example. Product manufacturers and importers should be prepared on how best to respond to avoid the criticisms that Whirlpool faced as to its attitude to product safety.
- Seek legal advice when using non-disclosure agreements in the context of compensation payments made to customers affected by a safety issue. Whilst confidentiality agreements serve a legitimate purpose in protecting the confidentiality of a commercial settlement, they should be drafted carefully to make sure that they do not prevent customers from sharing information on safety issues with regulators and safety organisations.
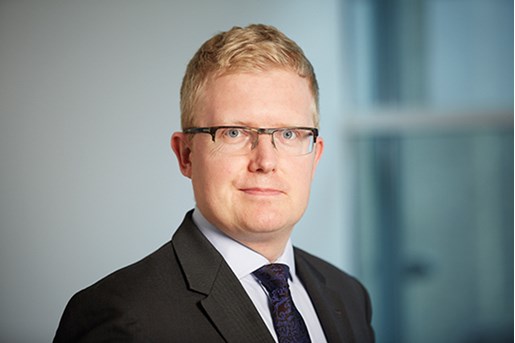
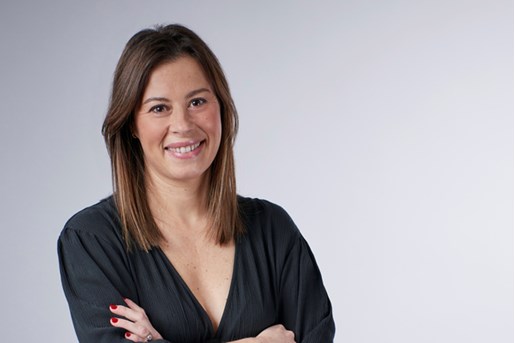