Find out what key decision-makers in the sector think about MMC.
Introduction
- What is currently done under MMC – student accommodation and some health, education and residential. Hallmarks of student accommodation which make MMC successful – less need to be flexible, need for volume (annual influx of student), tight timeline so need to agree design in advance, critical delivery dates.
- Interesting from an ESG angle – helps to developers reaching their targets.
- Issues – historic prejudice, lender caution (conservative and putting money into offsite facilities) and end server mortgage finance.
- Divided market – concerns about being last in line when urgency of project is squeezed and you aren’t the largest client (although this can be dealt with in contract drafting). Developers want control and may prefer their own product rather than using third parties.
- Protection for funders could increase the viability using warranties and third party contracts. Stimulation to the market from investors, getting money from government simply to get the market running.
- The model needs to be proven and doesn’t cause long term defects.
- What is MMC?
-
Wider than modular – also about methods of construction not just assembly or unit types. Simply moving away from doing things on site but doing larger builds offsite and assembling onsite.
-
The Government defines MMC as three distinct (but linked) areas – modular (volumetric), component (floors, shower rooms etc.) and manufactured.
-
There are huge variations between suppliers ranging from timber frame right through to full volumetric and there is a lot of jumping on the MMC bandwagon. There is an element of horses for courses, you need to look at the end goals and find the right solution.
- MMC Role In Net Zero:
-
How is net zero carbon measured? Is it net zero in operation and/or carbon offset through construction?
-
Some building systems would have payback which wouldn’t be realised at Day 1. How to measure, and then sell the benefits to the market
-
Performance in use and, the measure for that is to achieve a SAP rating of 100+
-
Manufacturing offsite is easier to reach net zero carbon goals.
-
As the environmental agenda gains greater prominence in the boardroom, this could/should play into the hands of the MMC industry. The ESG requirements are making people pay real attention and not just lip service. But ultimately viability, funding and cost still have a powerful place in the decision making process.
-
- Place Making:
-
Placemaking is no less important for developments carried out via MMC. Stigma leads to fear that ‘standardised housing’ will lead to bland places. Victorian neighbourhoods are proof that this isn’t the case. As ever it is about master planning, not isolated site development
-
Tackling emotional as well as economic challenge.
-
Focus on multi-tenure housing and government help schemes. Diversity of tenure is key for creating vibrant "places".
-
MMC can be used to help address challenges around delivering affordable housing which is also high quality.
-
- Quality:
-
Built offsite and delivered with far fewer defects than a conventional build.
-
Tension between standardisation and customisation.
-
Snagging and defects can be reduced by using MMC. L&G indicated, for example, that they are currently at 5 defects per unit/home but aim to get to 0.
-
Standardisation is desirable. Will reduce cost and defects and enhance viability and further enhance certainty re delivery and installation
-
Defect minimisation is streets ahead of traditional construction.
-
- Skills:
-
Skills for those to execute modular well are not traditional e.g. bio-pharmacy company who have experience of driving quality and design. "Turnkey" healthcare buildings can be delivered by MMC (c.f. Northumbria Healthcare Facilities Management successful projects), but requires different skills and collaborations
-
There is a dichotomy with MMC suppliers between being a ‘manufacturer’, versus being a ‘contractor’ and taking on other areas like ground works and externals. Is there enough expertise in all areas to allow multiple projects across the country to successfully delivered?
-
The national skills shortage has a big part to play - sub-contractor availability and quality is a huge issue with onsite construction. MMC is a great opportunity to up skill workers and create a better quality workforce.
-
- Can Modular Meet The Demand In Housing Capacity:
-
100,000/150,000 units a year have been delivered since the war using traditional methods – this is likely the only way to deliver the supply needed.
-
Obvious gap, but also obvious opportunity. Greater support from central government desirable, but also improved viability and certainty of funding
-
- Sustainability Of The Model:
-
There is a need for consolidation. Anecdotally there are a lot of local producers operating on a small scale. Economies of scale needed to really make a different so the market will have to respond with consolidation and collaboration.
-
Customer (both landowner/developer and end user) scepticism and ignorance needs to be overcome. In general challenges of getting the market to recognise the value of the product. Better education and better promotion needed.
-
It is about more than construction – it is about infrastructure and systems to lead to the development. Perennial problem with development, but even more so when a zero carbon/carbon neutral scheme is desired.
-
Integrated solution required to manage the risk and get the different skills input.
-
Type of returns investors are looking for will impact success of MMC – other models could work such as lending to local authorities or leasing homes with the site being owned by funder. Longer term investment horizon will aid viability e.g. 5% developer return over 20+ years is easier to fund than 20% immediately.
-
Also need to understand what part(s) of the process are to be funded – product only, factory to delivery, installation, development. Different funders may be attracted to different aspects.
-
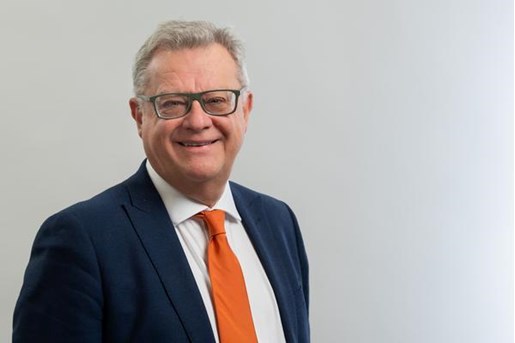
Michael O'Connor
Partner, Chair of Government Contracting Group, Co-head of Healthcare Sector
United Kingdom
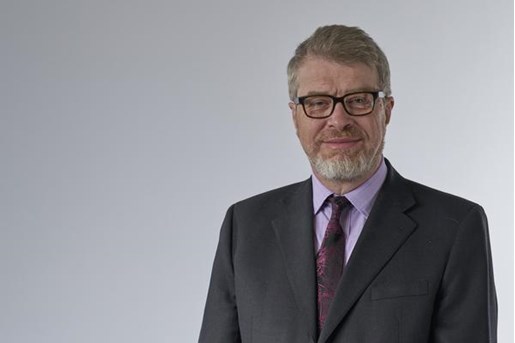
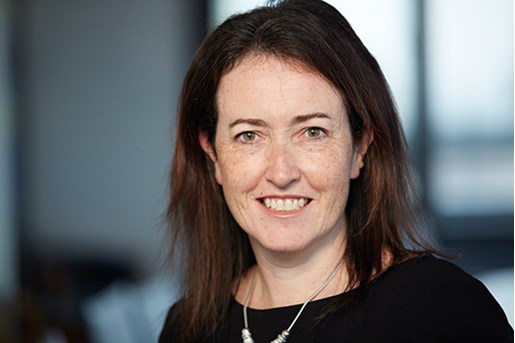
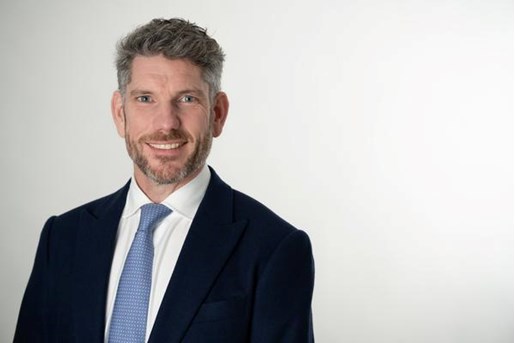